Precision sheet metal work might not be the most glamourous of manufacturing processes, but it lays the foundation stone for a myriad of products that we use daily, from electronic enclosures to aerospace components.
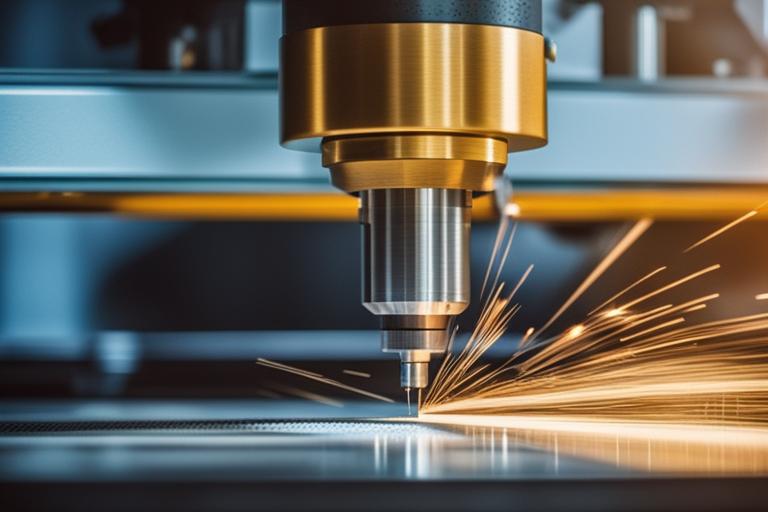
In this detailed blog post, we will dissect the impressive world of precision sheet metal to understand the complexity of this craft, the importance of its precision in product development, and some key trends shaping the industry.
The Art of Forming
The process of precision sheet metal is essentially the forming and cutting of a sheet metal to create objects including enclosures, brackets, chassis, and many more. What makes this process so vital is its ability to produce parts with high degrees of accuracy.
It all starts with the design, which has to be meticulously detailed to account for the incorporation of features that ensure the strength and functionality of the final product.
The fabricator must then select the right materials, commonly aluminum, steel, or copper, and proceed with cutting, bending, and assembling the metal. Each step requires precise measurement and execution to ensure that the final product meets the standards required by modern-day technology.
Quality Check: The Pulsing Heart of Precision
Measuring the quality of sheet metal parts involves several stages. The first is inspection of the raw material for surface defects as well as thickness and hardness tests to verify they are within the specified tolerances.
After the manufacturing process, the formed parts are checked with a coordinate measuring machine (CMM) that can detect any deviations from the expected dimensions.
Given that these components often serve as structural and functional elements within larger mechanisms, it is paramount that they are tested for durability, stress resistance, and snap fits where applicable.
Innovations and Trends in Precision Sheet Metal
The precision sheet metal industry is not immune to the rapid progress of technology. Here are some trends and innovations that are currently shaping the industry:
Robotics and Automation
The use of robotics has significantly increased the speed and accuracy of repetitive tasks. Robotic arms assist with bending, welding, and material handling, providing a level of precision that's hard to achieve consistently with human labor alone.
3D Printing of Sheet Metal
While 3D printing is typically associated with plastic, advancements have made it possible to print metal parts directly, reducing the need for multiple manufacturing steps and minimizing material waste.
Digital and AI-Integrated Manufacturing
Digital manufacturing technologies like the Internet of Things (IoT) and AI are enabling predictive maintenance, real-time quality control, and adaptive manufacturing processes. AI-optimized processes can analyze vast data sets to refine techniques and minimize errors.
Sustainability Through Lean Manufacturing
The industry is trending towards more sustainable practices by adopting lean manufacturing methodologies to reduce waste and energy consumption. Tools such as value stream mapping help identify opportunities for improvement.
Precision sheet metal continues to be an integral part of the modern manufacturing landscape. Its influence can be seen across numerous sectors, where high-quality components are the linchpin of progress and innovation.
While the future promises disruptions through cutting-edge technology, the foundational principles of precision and quality will remain unchanged. The artisans of precision sheet metal will continue to uphold these values, ensuring that the products of today and tomorrow are built to last.